Outdoor Lighting a Challenge Bested
One of AFS Corporate Member Powercast’s long-term customers in the lighting industry developed a concept for a fixture that would not only stand out with its elegant design, but also blend in perfectly with its surroundings and provide cutting-edge technology.
The cone-shaped fixture resembles a tree, and while its design stands out, it was not planned for manufacturability. The concept proved to be a challenging project for Powercast (St-Eustache, Quebec, Canada), but by working closely with the customer, they kept the design intact while adapting it to the permanent mold process.
Powercast general manager Ravi Gupta said it was determined early that metalcasting would be the best process for the project, since assembling or welding several castings together would not have been feasible.
“Going with a permanent mold casting would provide the best value in terms of respecting the design as much as possible,” Gupta said. “The overall cost, ease of machining, ease of assembly and paint, surface finish and dimensional accuracy (were also factors).”
The design was created with an organic-looking lighting fixture in mind—one that would blend into a typical urban setting. The concept was proposed and approved by the customer’s marketing department. It was then handed to the customer’s engineering team responsible for new products, with almost no room for design changes in order to keep the original concept intact.
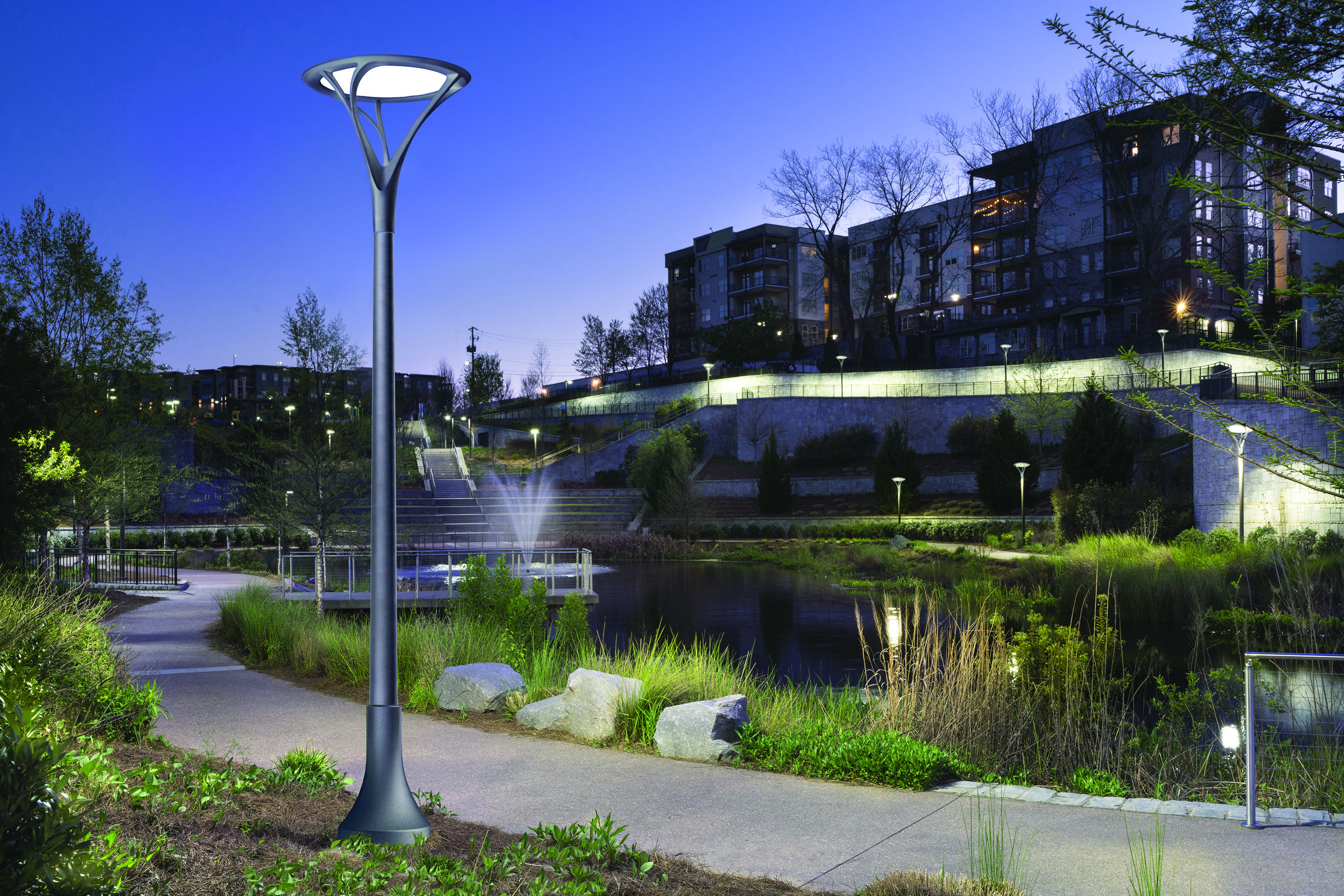
The engineering team then turned to Powercast for assistance in discussing the fabrication of this part, specifically as a casting. Many hours were spent in in-person and online meetings, discussing the intricacies of the component until the final casting drawing was finalized.
“The casting allowed the customer to replicate the required design as closely as possible,” Gupta said. “Going with a one-piece casting also eliminated the options of welding different parts together, and replicated very closely the original concept, with its seamless design, graceful curves and tree-like branches.”
It didn’t hurt that Powercast and the customer had a long-term relationship.
“Having worked closely on other complex designs before, we were asked to help with the casting design right at the start, which is the optimal timing to begin reviewing a potential casting,” Gupta said.
That doesn’t mean the project was easy.
The shape of the component was challenging. The part has thin sections, undercut areas, and various precise features necessary for post-casting machining and assembly of LED components. The pouring height, how to pre-heat the tool and warpage were among the issues Powercast had to overcome through experimentation and trial and error.
“Ultimately all these challenges were addressed by our team as a group effort, through many brainstorming meetings, disagreements and agreements, and challenging each other’s ideas,” Gupta said. “All of this led to a commonly agreed-upon consensus as per how to proceed. Every aspect of the process was discussed: how to design the tool, what materials to use, how the feeding/riser/ejector systems were going to function. How the operators were going to pour this casting, how it was going to be cut, grinded, finished and packaged.”
The customer provided various 3D-printed sections of the part and glued them together to create a life-sized model. After that, the customer requested sample castings in aluminum. Powercast produced plaster molding casting samples, which replicated the eventual appearance.
Click here to see this story as it appears in the June 2019 issue of Modern Casting.